LEAN MANAGEMENT IN QUALITY MANAGEMENT: EFFICIENCY MEETS EXCELLENCE
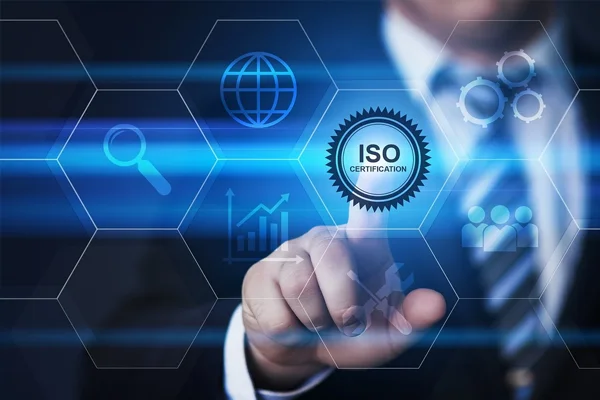
Quality management (QM) is a central element of successful corporate management. It aims to systematically improve processes, products and services in order to fulfil customer requirements in the long term.
In recent decades, lean management has established itself as an effective method for combining efficiency and quality. But how can lean principles be applied in quality management, what are the benefits and what challenges do companies have to overcome?
WHAT IS LEAN MANAGEMENT?
Lean management (often also referred to as ‘lean management’) is a management concept that originated in the automotive industry (particularly at Toyota). The aim is to create added value without waste (muda) - in other words, to design processes in such a way that they are optimised to meet the needs of the customer while using as few resources as possible.
The five core principles of lean management are
- Define value (from the customer's perspective)
- Analyse value stream (identify all steps that contribute to value creation)
- Create flow (design processes without interruptions)
- Introduce pull principle (production according to demand instead of stock)
- Strive for perfection (continuous improvement, Kaizen)
LINK BETWEEN LEAN MANAGEMENT AND QUALITY MANAGEMENT
Although lean management originally aims for efficiency, it ideally complements the concept of quality. While classic quality management (e.g. according to ISO 9001) sets structural and documentary requirements, lean focusses on dynamic methods for continuous improvement.
COMMON GOALS OF LEAN MANAGEMENT AND QUALITY MANAGEMENT:
- Error avoidance instead of error correction
- Customer focus
- Process stability and transparency
- Culture of continuous improvement (CIP/Kaizen)
LEAN TOOLS IN QUALITY MANAGEMENT
1. 5S-Method
A structured approach to workplace organisation:
- Sort (Seiri): Remove unnecessary things
- Systematise (Seiton): Everything has its place
- Cleaning (Seiso): Order and cleanliness
- Standardise (Seiketsu): Create rules
- Self-discipline (Shitsuke): Promote discipline and responsibility
→ Result: fewer mistakes, clear processes, more quality
2. POKA YOKE (ERROR PREVENTION)
Techniques that prevent human error - e.g. through mechanical safeguards, visual cues or software validation.
→ Result: drastic reduction in errors
3. ANDON-SYSTEM
Visual signals (e.g. lights or displays) immediately indicate faults or quality problems so that an immediate response can be made.
→ Result: faster troubleshooting, shorter downtimes
4. ROOT CAUSE ANALYSIS
For example, using the 5 Why method or Ishikawa diagrams to sustainably eliminate the causes of faults instead of just treating symptoms.
→ Result: sustainable quality improvement
5. STANDARDISED WORK
Documented best practices secure knowledge, facilitate training and reduce fluctuations in product quality.
→ Result: consistency and reliability
ADVANTAGES OF LEAN IN QUALITY MANAGEMENT
The application of lean management in quality management brings with it a multitude of advantages. By consistently avoiding waste and standardising processes, error rates can be significantly reduced. At the same time, lean processes enable shorter throughput times, which increases both responsiveness and efficiency within the company. A direct consequence of this is increased customer satisfaction, as products and services can be delivered faster and with consistently high quality. In addition, the lower error and rework costs lead to considerable savings potential. Another key advantage is the greater involvement of employees in continuous improvement processes. They are seen not only as performers, but also as active creators of quality. Overall, lean in quality management not only improves product quality, but also the corporate culture and long-term competitiveness.
CHALLENGES IN IMPLEMENTING LEAN MANAGEMENT IN THE COMPANY
Cultural change required: Lean demands a change in thinking from management and employees - mistakes are not punished, but analysed.
Initial effort: The introduction of lean tools requires resources, training and time.
Danger of ‘lean-washing’: Lean is not a pure efficiency programme - without a focus on quality and people, it remains ineffective.
Interdisciplinary co-operation: quality management, production, purchasing and development must work hand in hand.
PRACTICAL EXAMPLE: LEAN QM IN THE AUTOMOTIVE INDUSTRY
A supplier in the automotive industry integrated lean principles into its QM system. By introducing 5S, daily shop floor meetings and root cause analyses, the complaint rate was reduced by 60% within a year. At the same time, throughput times fell by 25% and employee motivation increased as suggestions for improvement were systematically recorded and implemented.
PeRoBa Quality Management from Munich - Individual Quality Management and ISO Consulting
Consulting, implementation, audits and QM tools from a single source
PeRoBa GmbH Munich is a service provider with many years of experience in quality management, especially in automotive and mechanical engineering.
We show you how to actively counteract ISO certification disadvantages.
We look forward to hearing from you. The best way to reach us is by phone at the number
+49 8106 / 230 89 92
(more
contact options)
Quality management
ISO 9001, VDA 6.3 and IATF 16949 - www.peroba.org